- Products
- Commercial divers’ equipment
- Compasses and watches
- Defence divers’ equipment
- Diving instrumentation
- Electrical diving equipment
- Escape and abandonment
- Gas and fluid systems
- Medical and safety equipment
- Recompression chambers
- Submarine intervention
- Submarine rescue
- Tactical Diving Vehicles
- Ansti testing equipment
- Services
- Consultancy and personnel
- Engineering services
- Rescue and support
- Testing services
- Training services
- Ancillary dive gear
- Commercial equipment and tools
- Commercial helmets, masks and SCUBA
- Commercial rebreathers
- Commercial surface supply
- Diver's suits and harnesses
- Contaminated water diving system
- BIBS manifold block
- Divex back pressure regulator
- Divex interlock
- Hy-Fex hyperbaric fire extinguisher
- Hyperbaric flame detector
- Hyperlite hyperbaric stretcher
- Oxygen kits
- Ultralite 2 BIBS mask
- InVicto ventilator system
- DSAR rescue vehicles
- Launch and recovery systems
- Multi-role launch and recovery system
- Submarine rescue bell
- Client representatives
- Dive and ROV system audits
- Diving technical expertise
- Offshore personnel
- Rescue certification
- Remote audit solution
- Altitude testing and trials
- Hyperbaric welding
- Pressure testing and trials
- Test tank
- Breathing laboratory
- Commercial development courses
- Defence training courses
- Medical training courses
- Product specific courses
- Online training courses
- Classroom training FAQ
- Case Study: Roger Chapman Pisces III
- Case Study: HMS Edinburgh
- ANSTI CSTF
- Akademik Tofiq Ismayilov (ATI)
- Archive
- JFD strengthens Commercial Diving business with leadership appointments
- JFD unveils new product concept ‘Stealth Multi-Role’ at key industry events
- JFD North America enhances US Navy Submarine Rescue capabilities with advanced Integrated Communication System
- JFD successfully integrates and delivers advanced submarine rescue system for Republic of Korea Navy
- Archive
- Divulged - Winter 2017
- Divulged - Summer 2017
- Divulged - Winter 2016
- Divulged - Summer 2018
- Divulged - Winter 2018
- Divulged - Winter 2019
- Divulged 2021 Edition 1
- UDT 2019
- Visit JFD at UI 2016
- Visit us at OTC Asia 2018
- Visit JFD on stand 338 at Underwater Intervention 2018
- JFD is exhibiting at ONS 2018
- JFD is exhibiting at OSEA 2018
- Join JFD at IDEX 2019
- See JFD at Subsea Expo 2019
- JFD takes on BALT Military Expo
- JFD presents complete defence offering at UDT 2018 in Glasgow
- Join JFD at ADIPEC 2018
- Visit JFD at Pacific 2017
- Visit JFD at MSPO 2018 in Poland
- JFD presenting at UDT conference
- JFD is exhibiting alongside James Fisher Nigeria at NOG
- JFD exhibiting at UDT 2016
- Visit JFD at Underwater Intervention 2019
- JFD is participating at Underwater Defence & Security
- See JFD at this year’s IMCA Annual Seminar
- JFD is exhibiting at LAAD Defence & Security 2019
- JFD LEXMAR is exhibiting at OSEA 2016
- JFD is exhibiting at Subsea Expo 2017
- Visit JFD at Indo Defence 2018 Expo and Forum
- Visit JFD on stand 403 at Underwater Intervention 2017
- JFD exhibiting at Europoltech
- JFD at IMDEX
- Visit JFD at UDT 2017
- Visit JFD at DSEI 2017
- JFD is exhibiting at OTC 2018
- JFD is exhibiting at Subsea EXPO 2018
- JFD is exhibiting at Sea Air Space 2018
- Visit JFD at DSA 2018
- See JFD at Defexpo 2018
- JFD is exhibiting at ADIPEC 2017
- Come see JFD at DSEI!
- See JFD at IMDEX Asia 2019
- JFD is at Oil & Gas Asia 2019
- Experience DSEI with JFD
- See JFD's full defence capability at MSPO 2019
- JFD is exhibiting at this year's Offshore Europe
- Visit us on stand 2S16 at Pacific
- See JFD at ADIPEC on stand 13572
- Explore our commercial capabilities at Bergen International Diving Seminar
- JFD showcasing commercial and defence capabilities at Underwater Intervention
- JFD exhibiting alongside James Fisher Offshore at Subsea Expo
- Visit our stand at DSEI 2021!
- Join JFD at Subsea Expo 2022
- Visit JFD Australia at Indo Pacific 2022
- JFD North America is exhibiting at SOFIC 2022
- Experience CNE 2022 with JFD
- Discover JFD at UDT 2022
- Join JFD at GSOF Symposium Europe this October
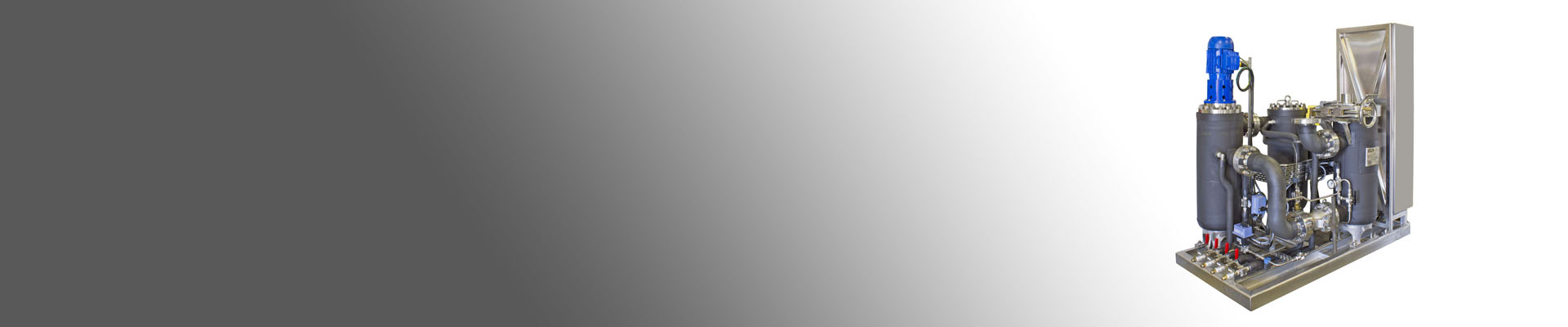
Hyperbaric conditioning unit
JFD's hyperbaric conditioning unit - external regeneration (HCU-ER) conditions the internal atmosphere of a saturation diving complex to maintain a habitable environment.
The external regeneration system provides increased diver comfort by having the system placed outside of the living chambers.
The HCU-ER HCU100 series offers uninterrupted operation through its twin scrubber design, enabling the change out of chemical absorbent whilst maintaining habitat conditioning capability.
The HCU-ER HCU100 series extracts gas from the chamber into the active scrubber, injecting additional moisture to improve scrubbing capacity. The gas passes through the chemical absorbent which retains any CO2 present in the gas.
Gas is then transferred to the dehumidifier where it passes over a cold water coil. This coil has the effect of lowering the gas to a temperature below its dew point; reducing relative humidity and enabling the collection of condensation in the dehumidifier sump.
The 3-stage blower then accelerates the gas into the heater where a hot water coil increases the gas temperature. The fully reconditioned gas is then circulated back into the chamber.
Local control via HMI allows the operator to view at a glance chamber temperature, humidity, blower speed and alarms; as well as establish set points for these criteria and run system tests. Essential to the operation of the HCU-ER is the supply of 440VAC, 3~, 60Hz, which is transformed and rectified to 24VDC by the integral HCU transformer.
|
|
Design depth |
350 msw |
PV design code |
PD5500:2006 |
Construction |
316L stainless steel |
Max no of occupants supported |
6 compressed divers |
Min operating depth |
0 msw |
Max operating depth |
350 msw |
Working pressure |
35 bar |
Test pressure |
46 bar |
Design temperature |
-20ºC to 80ºC |
Gas outlet |
3” ANSI B16.5 class |
Gas reclaim |
1/2” FNPT |
Hot water inlet |
3/4” FNPT |
Hot water outlet |
3/4” FNPT |
Cold water inlet | 3/4” FNPT |
Cold water outlet | 3/4” FNPT |
Water injection |
1/2” FNPT |
Drain line |
1/2” FNPT |
CO2 scrubber |
|
Capacity |
17.6 kg (8.8 kg per basket) |
3-stage variable speed blower |
|
Max Rpm |
7000 Rpm |
Gas flow |
2.8 m3/min-1 |
Dehumidifier |
|
Cooling capacity |
Max 10 kW |
Water removal |
780 ml/hr at 50% RH |
Heater |
|
Heating capacity |
Max 10 kW |
Controls |
|
Temperature control |
22ºC to 32ºC +/- 1ºC |
Humidity control |
40% to 65% RH +/- 5% |
Dimensions HCU100BA |
|
Length |
2000 mm |
Width |
1200 mm |
Height |
1850 mm |
Weight |
1400 kg |
Hot water requirement |
|
Min flow |
20 Lpm |
Min temp |
60ºC |
Min pressure |
4 bar |
Cold water requirement |
|
Min flow |
20 Lpm |
Min temp | 2ºC |
Min pressure |
4 bar |
Fresh/potable water requirement |
|
Min flow |
5Lpm with 10μm filtration |
Min temp |
Ambient |
Min pressure |
45 bar |
Power requirement |
|
Power requirement |
440VAC, 3~ , 60Hz |
Item | Order Code |
Hyperbaric conditioning unit – external regeneration (HCU-ER) single scrubber |
HCU100BA |
Document | Document type | Download |
Hyperbaric conditioning unit - external regeneration HCU-ER |
Datasheet | |
Hyperbaric conditioning unit - external regeneration HCU-ER - single scrubber pot, 350 msw (HCU100BA series) |
Operation and maintenance | HCU100-OM-6739 R0 |
The HCU-ER HCU100 series extracts gas from the chamber into the active scrubber, injecting additional moisture to improve scrubbing capacity. The gas passes through the chemical absorbent which retains any CO2 present in the gas.
Gas is then transferred to the dehumidifier where it passes over a cold water coil. This coil has the effect of lowering the gas to a temperature below its dew point; reducing relative humidity and enabling the collection of condensation in the dehumidifier sump.
The 3-stage blower then accelerates the gas into the heater where a hot water coil increases the gas temperature. The fully reconditioned gas is then circulated back into the chamber.
Local control via HMI allows the operator to view at a glance chamber temperature, humidity, blower speed and alarms; as well as establish set points for these criteria and run system tests. Essential to the operation of the HCU-ER is the supply of 440VAC, 3~, 60Hz, which is transformed and rectified to 24VDC by the integral HCU transformer.
|
|
Design depth |
350 msw |
PV design code |
PD5500:2006 |
Construction |
316L stainless steel |
Max no of occupants supported |
6 compressed divers |
Min operating depth |
0 msw |
Max operating depth |
350 msw |
Working pressure |
35 bar |
Test pressure |
46 bar |
Design temperature |
-20ºC to 80ºC |
Gas outlet |
3” ANSI B16.5 class |
Gas reclaim |
1/2” FNPT |
Hot water inlet |
3/4” FNPT |
Hot water outlet |
3/4” FNPT |
Cold water inlet | 3/4” FNPT |
Cold water outlet | 3/4” FNPT |
Water injection |
1/2” FNPT |
Drain line |
1/2” FNPT |
CO2 scrubber |
|
Capacity |
17.6 kg (8.8 kg per basket) |
3-stage variable speed blower |
|
Max Rpm |
7000 Rpm |
Gas flow |
2.8 m3/min-1 |
Dehumidifier |
|
Cooling capacity |
Max 10 kW |
Water removal |
780 ml/hr at 50% RH |
Heater |
|
Heating capacity |
Max 10 kW |
Controls |
|
Temperature control |
22ºC to 32ºC +/- 1ºC |
Humidity control |
40% to 65% RH +/- 5% |
Dimensions HCU100BA |
|
Length |
2000 mm |
Width |
1200 mm |
Height |
1850 mm |
Weight |
1400 kg |
Hot water requirement |
|
Min flow |
20 Lpm |
Min temp |
60ºC |
Min pressure |
4 bar |
Cold water requirement |
|
Min flow |
20 Lpm |
Min temp | 2ºC |
Min pressure |
4 bar |
Fresh/potable water requirement |
|
Min flow |
5Lpm with 10μm filtration |
Min temp |
Ambient |
Min pressure |
45 bar |
Power requirement |
|
Power requirement |
440VAC, 3~ , 60Hz |
Item | Order Code |
Hyperbaric conditioning unit – external regeneration (HCU-ER) single scrubber |
HCU100BA |
Document | Document type | Download |
Hyperbaric conditioning unit - external regeneration HCU-ER |
Datasheet | |
Hyperbaric conditioning unit - external regeneration HCU-ER - single scrubber pot, 350 msw (HCU100BA series) |
Operation and maintenance | HCU100-OM-6739 R0 |